昆钢远程集中计量系统
重构计量流程 提高管理效率
昆明钢铁控股有限公司(以下简称“昆钢”)始建于1939年,经过多年转型发展,已逐步形成传统产业和新兴产业相结合的现代企业集团,钢铁主业已形成年产1000万吨钢的综合生产能力。
一、背景情况
昆钢原有计量工作采取的是离散计量方式,即在生产现场必要的地方设置计量点、安装计量设备以及其他辅助设施后,派驻专人在现场进行值守作业,存在从业人员多、工作繁重、物流压力大、防作弊手段有限、现场噪声、粉尘、废气等对职工的身体健康造成不利影响等诸多问题。为此,昆钢从2009年开始开发、建设和推广远程集中计量系统。
二、技术措施
1.计量管控大厅建设(见图1)
计量管控大厅布置30个工作台位,覆盖44台秤的远程集中计量操作功能,同时配置了投影仪和金属硬屏用于全面展现现场计量环境和动态反映生产情况,具备了计量工作集中管控与调度功能。
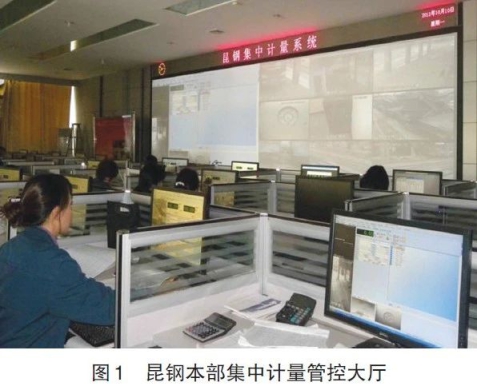
2.计量流程重构
整合了生产工艺流程、运输调度、计量预报、过重、取样、卸货、除皮、验收、ERP接口与运费结算等环节,并根据物料的不同进行具体流程细化,包含矿石煤焦进厂、辅料进厂、动态轨道秤3个子流程。
3.计量过程管控一体化
通过一体化智能机柜、液晶显示屏、LED显示屏、数据采集卡、读卡器等高科技设备,既实现了数据(数字、视频与多媒体信息)的实时采集存储,又可以根据需要及时把信息反馈给用户。具备了智能集成控制、现场同步显示和远程实时监控等功能。
4.高新技术防作弊
采用了图片抓拍比对、计量过程多角度实时监控、计量数据防重复保存、IC卡闭环物流控制、计量过程曲线斜率监控报警、双红外对射防不完全上秤、汽车历史皮重报警、过秤重量超限报警等十余种技术。
5.视频、图像信息多媒体监控与存储
硬盘录像机通过安装在计量点的多个摄像头采集视频信息,传输到计量系统过秤界面并存储录像。数据保存时,系统自动抓拍,并将计量数据叠加到图像上一起存储到中心数据库,真实保存了计量现场的情况。当发生计量异议时,不仅可以查询计量数据及图片信息,而且能够调取录像还原当时的真实计量场景。
6.语音双向对讲
计量现场安装有音箱和拾音器,大厅配备有耳麦,通过硬盘录像机提供的全双工语音传输功能,实现了计量员与现场用户的双向实时交互。
7.计量数据Web查询
计量数据存储后,只要是在昆钢城域网范围内被授权的用户,可以像上网浏览网页一样轻松查询到所需的数据信息。
8.物流、信息流的协调统一
用户可以通过查询计量数据,准确把握原料库存情况,从而制定更加准确的生产计划;物流运输管理部门可以通过对历史数据的分析挖掘,得出一个相对固定的运输需求情况,从而动态制定运输计划与调拨车辆;通过计量相关信息的提前预报,缓解交通拥堵情况的发生,提高计量效率;由于计量点集成在同一平台上,当发生车辆排队等待计量情况时,计量管控大厅可以动态调配等待车辆到空闲计量点进行计量,从而提高了物流效率。
三、具体成效
1.提高了管理效率
系统建立实时动态物联网总线平台,支持质量计量系统的数据自动采集、保存、传输,即时将质量计量信息与生产、产品信息进行匹配。借助系统的有效稳定运行,提供相关的基础数据保障支撑,使生产组织、工艺控制和检验计量的管理效率显著提高。
2.提高了物流效率
系统实现质量计量信息与物流实时同步,使检验计量速度加快,缩短质检计量过程对物流的影响,提高各工序物料的周转效率。通过集中计量系统支持,计量点功能兼容互补,解决了传统计量方式下空、重车在不同计量点过秤遇到的各种难题。
3.促进了生产、产品经济技术指标提高
通过质量和计量信息的实时集成和与生产信息的融合管理,生产组织和工艺过程可根据实时提供的指标数据进行生产计划安排调整、工艺控制,提高对现场生产计划组织的针对性、灵活性和及时性,减少生产过程中因质量计量信息滞后造成的损失。或因成分波动时工艺调整不及时造成的废品,或高质量指标的钢坯轧制成低级别的钢材成品等,有效促进了生产、产品、消耗等经济技术指标的改善和提高。
4.提高计量的准确、可靠性,保证物资产品质量
集中计量系统现场仪表和计量管控大厅点对点数据传输,解决了干扰信号影响数据的问题。系统设置过秤重量判别功能,在过秤重量稳定时系统自动采集计量数据,不允许手工输入,也不能粘贴复制,避免人工操作偏差,保证计量结果准确和数据传输安全、可靠。计量过程全程视频监控和录像,图片查询和录像回放功能使计量过程具备了可追溯性。汽车衡设置红外对射装置和摄像头,防止车辆上秤不到位、司乘人员不下车过秤等影响计量结果的情况。系统保存每辆车过秤历史数据,形成比对数据库监控皮重并实现异常情况报警,防止冒用车牌除皮等作弊行为;过秤过程保存显示重量变化曲线,曲线突变可发现称量过程的异常;通过IC信息卡对进厂大宗原燃料等重要物资设置取样、验收、卸货等环节的确认程序,保证进厂大宗原燃料保质保量。通过远程打印秤单和标牌(签),与实物唯一对应,便于查询和追溯物资进厂及发货情况。
5.提高劳动生产率
质量系统分级递阶业务操作,使生产各环节的质量数据实现适时动态自动采集融合,适时在线传递、查询,自动生成分析报表,改变了人工抄录、传递、统计的工作模式,工作效率明显提高。计量系统远程站点无人值守,计量业务集中操作,改变传统计量方式站点分散,人员按点配置,人数相应较多且工作负荷不均衡的现象。实现了一人多点、一人多岗的优化配置,大大减少了人力配置,改善了工作环境条件。