建立起重机调试检测
计量模式 解决行业技术难题
徐州重型机械有限公司溯源于1943年许世友将军麾下八路军鲁南第八兵工厂,是中国工程机械行业历史最悠久的专业化生产企业。公司主营业务为轮式起重机的研发、制造与销售,现已成为领跑全球的轮式起重机制造商,数次引领行业变革。
一、背景情况
徐州重型机械有限公司作为起重装备行业的龙头制造企业,占据着国内市场约50%份额,但直面国际高端品牌竞争,在汽车起重机品质持续改进方面依然存在差距。汽车起重机整机调试是产品交付用户前的最关键质量管控环节,突破起重机调试在线检测与智能诊断关键技术,实现起重机质量评估与风险管控,是公司产品品质升级的迫切需求。但在起重机数据检测过程中,长期存在以下三大难题:
1.起重机具有机械、电气、液压与控制等多专业强耦合特征,传统整机调试依赖人员技能与经验,原有检测手段落后,无法对产品质量与性能指标严格量化,难以支撑品质跨越式提升。
2.起重机调试地域环境差异较大,需面临高温、极寒、潮湿等环境,传统调试试验标准主要对产品作业载荷、安全保护、基本参数要求进行了规定,而对产品系统性能特性缺乏普适性的量化标准,这也是传统依赖人工技能调试方式的固有缺陷。
3.传统的质量管控模式数据支撑不足,在PDM、MES、SAP及物联网等系统中存在大量异构数据,数据孤岛现象明显,造成质量问题暴露不全面,质量改进问题不清晰,浪费较多的人力物力。
二、技术措施
围绕专业化的检测设备、全面多维度的检测标准、数据挖掘及PDCA闭环应用,公司开发了行业首家移动式起重机线性化调试在线检测系统。
1.全球行业内率先构建基于“检测标准”的线性化调试在线检测单元,树立“智能制造”标杆
(1)构建基于“检测标准”的智能检测单元(见图1)
针对调试过程检测手段落后,质量数据可追溯性差的难题,创新研发了起重机调试在线检测设备50套,经国家计量技术机构检定,设备检测能力和准确度达到行业先进水平,质量控制精准度提升50%以上。
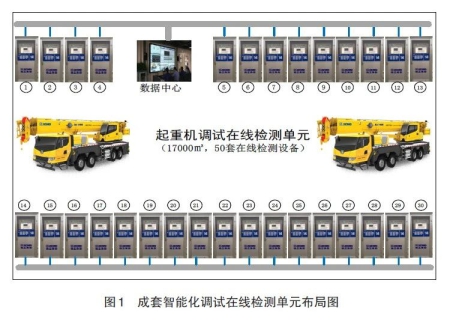
(2)研发智能化检测软件(见图2)
项目研发起重机智能调试软件,实现性能参数自动标定、数据自动评判等功能,实现整机作业性能参数的智能化评价,电控产品性能参数标定效率提升90%,市场参数调整类反馈降低60%以上。

(3)数据集控中心建设(见图3)
项目融合多协议交互通信技术、实时数据库差异化查询技术,建立起重机调试集控中心,实现对性能参数检测的实时监测及可视化统一管控,现场生产管理效率更高,数据可视化管理能力大幅提升。
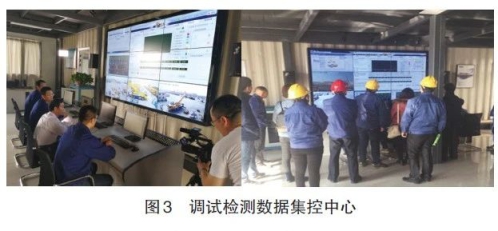
(4)开发基于GPS的吊臂幅度自动检测设备
面临传统依赖人工测量带来的效率低、准确度低、危险大的难题,开发基于GPS的吊臂幅度自动检测设备,实现力限器标定准确度由5%优化到4%,标定效率提升50%,与标杆利勃海尔水平相当。
2.行业内率先制定起重机性能评价指标及检测标准(见图4),完善了企业标准资源库,填补了行业空白
起重机产品系统性能可靠性测试方法和评价标准值的缺乏是行业面临的共同难题。目前移动式起重机行业涉及检测和试验方法的标准有近30个,这些标准主要对产品作业载荷、安全保护、基本参数要求进行了规范,而对产品系统性能、可靠性测试方法和评价标准值等方面没有具体规定,并且涉及产品整机主观评价模型和客观评价方法等内容的起重机标准几乎没有。

本项目通过选取20多款起重机产品作为测试对象,针对起重机产品的卷扬系统、变幅系统、回转系统、伸缩系统等15类9种系统近10000个工作工况,覆盖-40℃到90℃的各种系统环境,测试研究产品各系统的运行状态,总结产品性能的速度、微动性、平稳性、调速性等用户关注特性,形成移动式起重机25种系统性能评价指标近1000项,完善了企业标准资源库,填补了行业空白。
3.行业首创基于统计过程控制(SPC)的起重机整机质量闭环动态管控平台
创新研发了调试检测数据网络化管理模块,建立人、设备、数据、流程交互平台,实现数据化、智能化、可视化的统一;研发数据分析与挖掘等功能,实现性能参数自动统计分析和质量数据的闭环动态管控,极大提升数据可追溯性。
(1)调试质量数据SPC平台开发
国内起重机行业内普遍存在起重机整机调试过程数据积累、挖掘与利用能力不足、产品质量追溯性不强的现状。项目构建人员、设备,数据和谐交互的调试质量数据SPC平台,通过实时调用六西格玛Minitab软件,实现相关数据的图形、图表分析信息的多维度查询及可视化展示,数据有效利用率达到95%以上,填补了起重机行业整机性能数据挖掘与利用的空白,实现起重机质量从检测到预防的转变,达到国际先进水平。
(2)检测标准与资源网络化管控
基于VS和C#技术,开发标准网络化配置功能,实现调试检测标准库、评价程序库、传感器库的平台化网络化管控,包括检测标准、测点明细、检测指标、检测工况、模糊评估权重等,实现资源、数据的统一管理、互联共享。
公司通过突破起重机调试检测设备实时数据与后台信息系统关系型数据集成的技术,攻克PDM、ERP、MES及物联网等系统接口标准不统一的难题,从而构建起重机整机数据采集、质量分析、风险预测、数据追溯的信息化平台,实现起重机产品质量实时在线管控。
三、具体成效
围绕“智能制造”主题,针对起重机行业多品种、小批量的生产模式和机械、电气、液压与控制多专业强耦合的特点,完成起重机线性化调试在线检测体系建设,研发了调试检测设备50套及调试质量数据SPC平台1个,制定企业标准12个,解决了起重机行业普遍存在的整机调试检测手段落后、调试效率不高、调试数据缺乏追溯性的难题。
该项目已经实现在25款起重机质量控制中的应用,产品调试效率提升32%、市场超早期故障反馈率降低35%以上,新增利润7018.56万元/年,新增税收1754.64万元/年。
项目成果全球行业领先,起到了引领及示范作用,支撑了我国起重机行业整机调试与试验技术的创新发展,有效地推动了我国起重机行业产品质量提升与技术进步。
四、感受体会
起重机调试在线检测系统装置,构建了以“数据”和“标准”为核心的质量闭环管控模式,后续将继续围绕数据自动处理能力提升、数据挖掘能力提升两个方面,持续提升检测覆盖度和检测深度,优化起重机质量水平。
同时,将在起重机调试在线检测的基础上,修改起重机行业标准GB/T6068-2008《汽车起重机和轮胎起重机试验规范》,引领起重机行业的发展。起重机调试检测计量模式在工程机械领域内的其他行业起到了引领示范作用。